Polycarbonates (PC)

PC natural
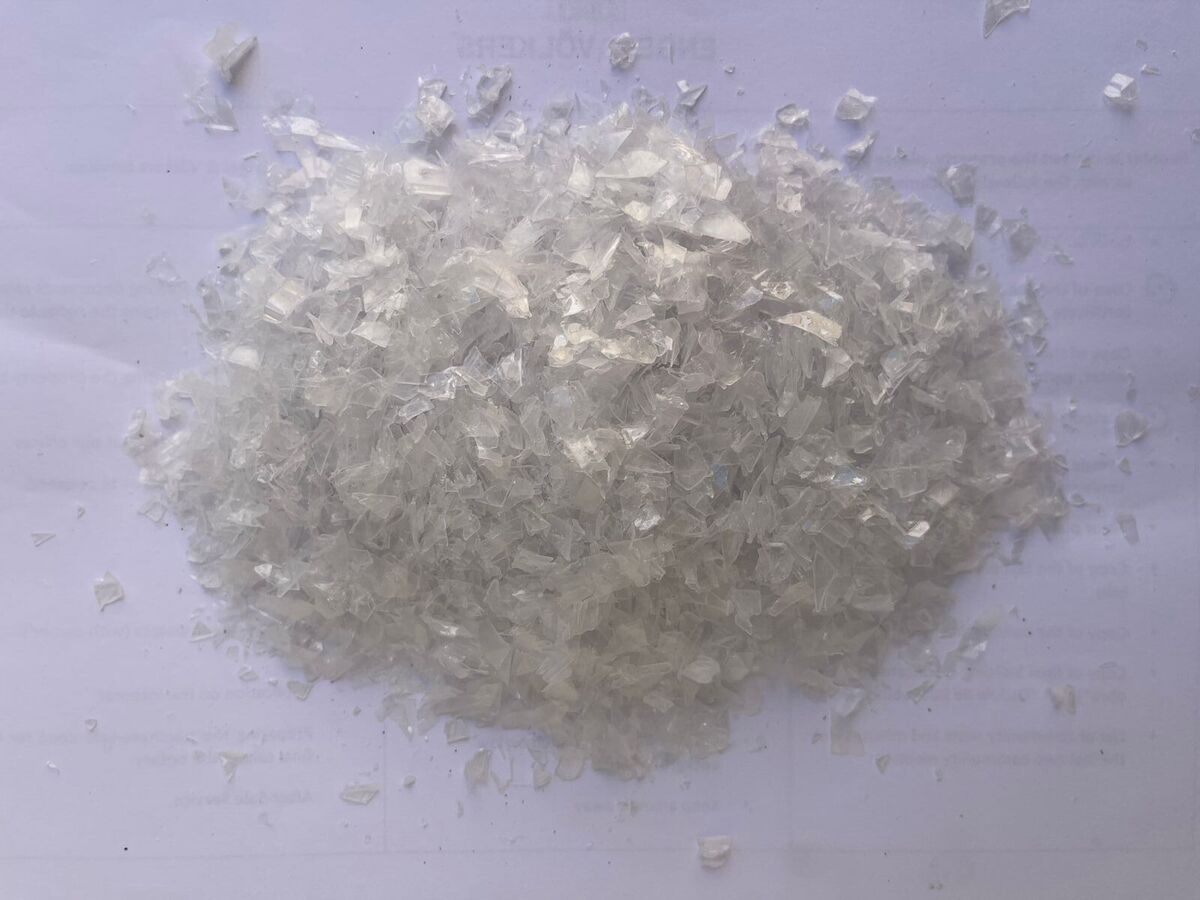
PC of bottles
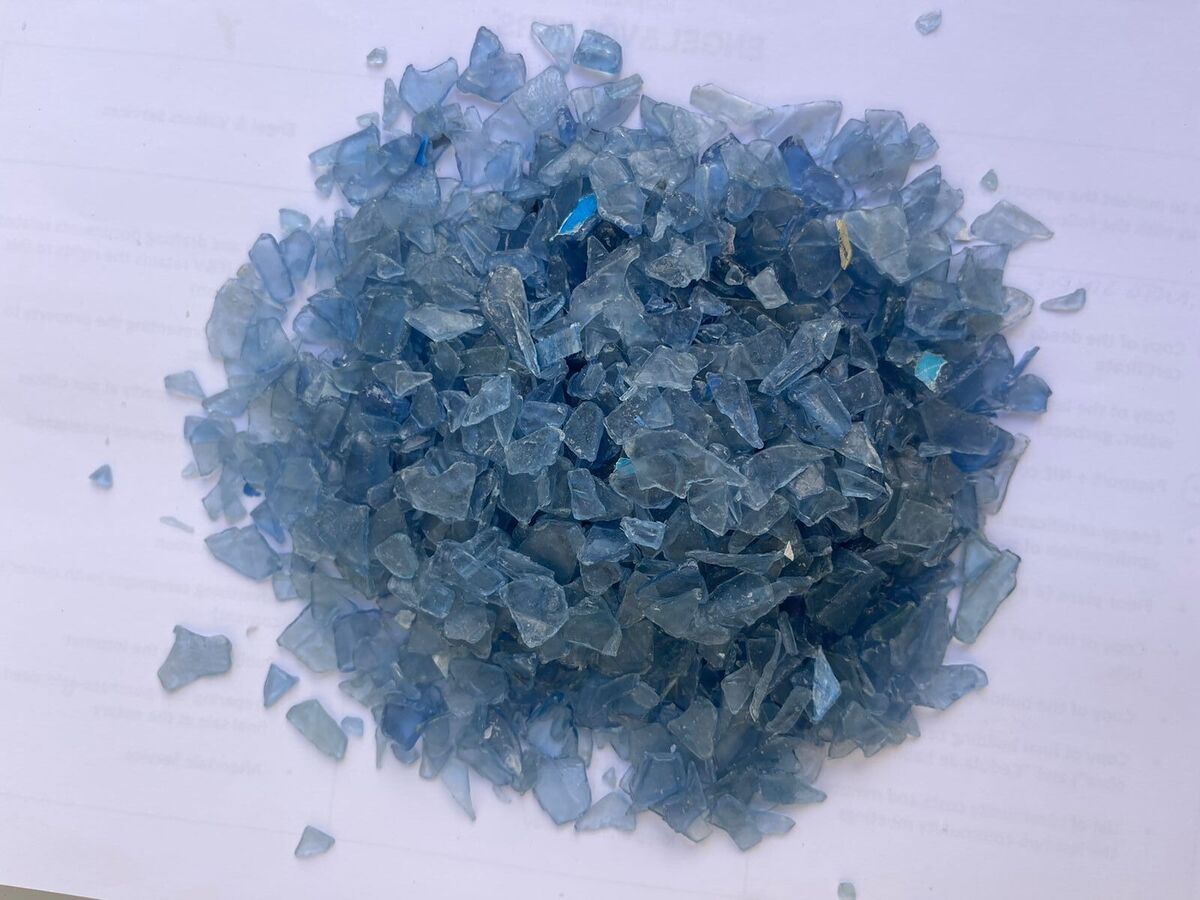
PC Tritan
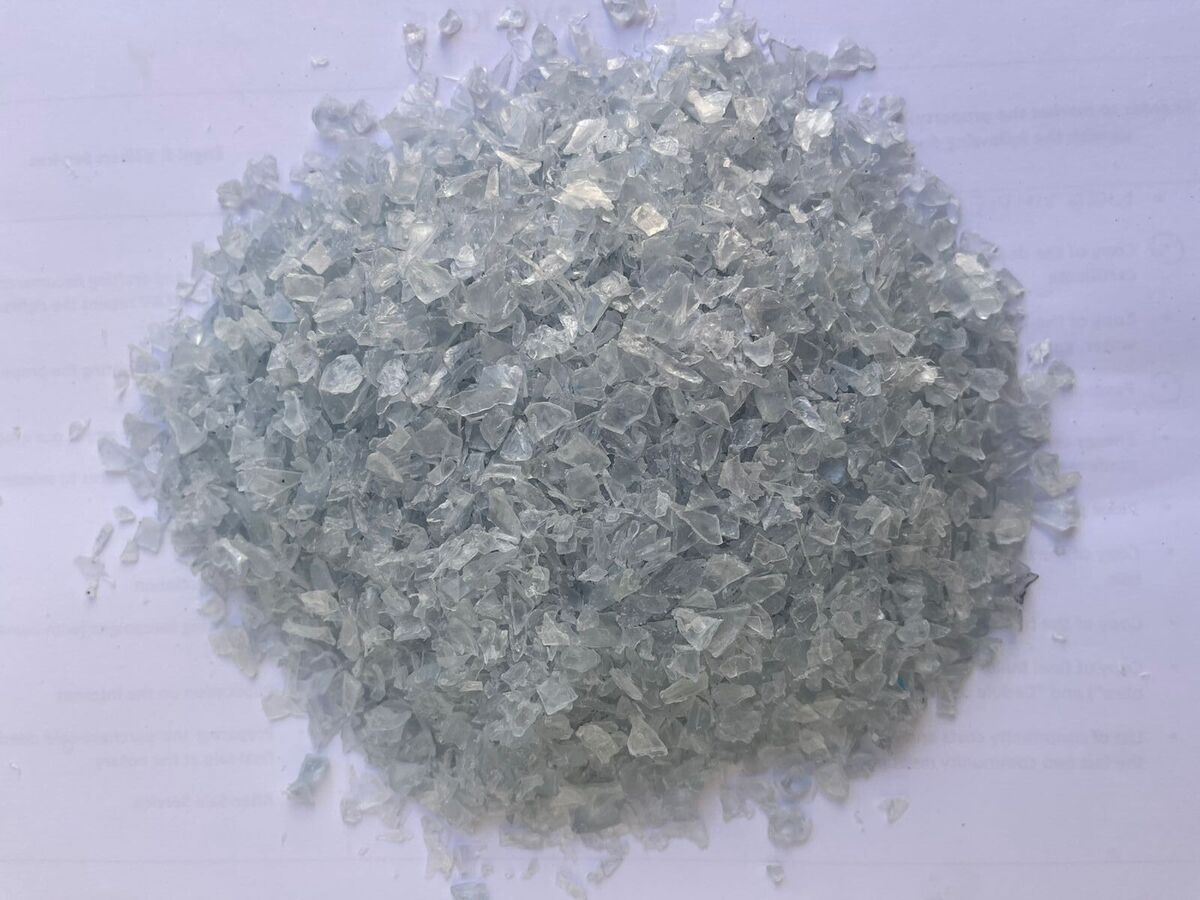
Product Overview
Polycarbonate is a plastic consisting of polymers that are formally esters of carbonic acid. It is a transparent material, although it can be painted in different colors. This is a thermoplastic that allows us to obtain products of various shapes and sizes.
Properties of polycarbonate
Polycarbonate has many valuable properties that make it an indispensable material in many industries. First of all, it is characterized by high impact strength, resistance to abrasion, moisture and low temperatures. Its features include resistance to breakage, allowing it to be used anywhere glass can work. Colored polycarbonate is also resistant to sunlight – its color does not fade under their influence. Its compressive strength is similar to that of aluminum.
Manufacturing process
Polycarbonate granulate arrives at the processing plant prepackaged in multi-layer moisture-proof bags. Granules are weighed and loaded for storage in silos; high warehouses with a conical, funnel-shaped bottom, through which raw materials are easily fed to the machine.
From the silos, the pellets are loaded into the cyclone using a pneumatic conveyor; a centrifuge-like device designed to clean raw materials from dust; any extraneous impurities can negatively affect the quality of polycarbonate sheets: impair their transparency, color or weaken their characteristics. Dust-free granules pass through an automatic dispenser and fall into the hopper; the chamber where their melting takes place. Various additives are added there to improve the properties of the mixture and future sheets, for example, to foam or prevent water condensation on the surface and inside the cells. Polycarbonate mixture melts in the hopper and is mixed, gradually heating up to 250; 290 degrees Celsius and turning into a homogeneous mass. The gases released during this process are led outside.
The next unit of the production line is the extruder. It forms the appropriate structure of the letter; monolithic or cellular. The use of an extruder is explained by the fact that polycarbonate, even in its liquid state, remains a highly viscous substance, and it is most effective to form flat sheets from it by pressing (extrusion) through a special matrix or die. This is how the product of the desired profile is obtained. Then the formed polycarbonate tape falls under the press, which gives it the required thickness and smoothness, and moves further along the conveyor, relaxing, that is, freeing itself from the acquired loads.
When the polycarbonate tape has cooled and assumed its natural shape, it is cut into sheets. Finished panels are placed on a pallet, experts use devices to check their quality: thickness, strength, light transmission, thickness of the UV protective layer, foreign inclusions. After that, the polycarbonate panels are taken to the warehouse on automatic loaders.